En nuestro pais, con el desarrollo de la ciencia y la tecnica, la vivienda ha llegado a ser cada vez mas amplia y confortable, desarrollando, desde la decada de los ochenta hasta la actualidad hellos y variados proyectos urbanisticos que sin duda han modemizado nuestras principales ciudades, sin embargo su elevado costo ha impedido a sectores mayoritarios acceder a estas, creando una polaridad significativa entre el habitat de unos y otros.
El concepto de vivienda económica tiene un caracter muy relativo, pues esta en relación directa con el poder adquisitivo de los futuros moradores, asi como de las condiciones de entrega y los plazos a cumplir en sentido general. Sin embargo, existen comunes denominadores que sin dudas constituyen los factores determinantes en este propósito, y que son los siguientes:
Precio de la tierra.
Disefio.
Tecnicas de ejecución.
Precio de la mano de obra.
Materiales empleados.
El tema que nos ocupa responde a este ultimo factor, es decir, a los materiales empleados. Con el desarrollo tecnológico, se fueron incorporando a la construcción de viviendas materiales de elaboración mas complejas que fueron encareciendo las mismas lo que unido a los otros factores, ha convertido de suefio en pesadilla la posibilidad de adquirir su casa propia a un sector importante de la población.
El presente trabajo expone abiertamente la producción y uso de nuevos materiales de construcción altemativos a partir de materias primas autóctonas, siendo estos una opción mucho mas austera sin menoscabo de los parametros a cumplir tanto de disefio como de ejecución, pues la calidad y vida util de la vivienda determina en gran medida para la familia su calidad de vida en general, de ahf la importancia social que representa lograr el acceso de la población a una vivienda digna pero a la vez económica.
En el presente trabajo expondremos la producción y uso de dos nuevos materiales: El aglomerante puwlana-cal y la pintura cementosa, estos, una vez implementados a nivel industrial podrían sustituir de inmediato a sus similares tradicionales produciendo un efecto económico importante, utilizandolo de esta manera en la construcción de nuevos proyectos habitacionales.
DESARROLLO
Aglomerante puzolana cal. (Cemento romano)
Sobre este tema nos proponemos exponer las experiencias relacionadas sobre estos aglomerantes, tanto en lo que respecta con su tecnologfa de producción como su empleo en la construcción, investigando ademas la factibilidad de uso de las materias primas requeridas existentes en el país.
Estos aglomerantes, cuyo origen se remonta a mas de 2700 afios y que con el surgimiento del cemento portland (patentado en 1824 por Apsdin) fueron desplazados gradualmente hacia lo que podríamos denominar la periferia marginada del desarrollo tecnológico, lo cual ha constituido un grave error de naturaleza tecnico-económica, comenzando a superarse en los ultimos tiempos, objetos de una gran atención hoy dfa no solo en los países en vías de desarrollo sino tambien en aquellos industrializados convirtiendose cada vez mas en un recurso indispensable para la construcción ante la sostenida y creciente escasez de recursos energeticos en la mayorfa de los países del planeta y del fuerte impacto queen los costos tiene la energía en la producción de cemento portland, mas aun el acuciante y al parecer insoluble problema de la vivienda.
En las condiciones actuales en nuestro país con restricciones energeticas en particular y económicas en general, el empleo de estos aglomerantes de bajo consumo energetico, tecnologfa de producción sencilla y muy bajo costo de producción, se hace una necesidad ineludible, maxime cuando no se trata solo de sobrevivir sino min en estas diffciles circunstancias, proseguir nuestro desarrollo.
Ante la gran demanda energetica necesaria para la producción del cemento portland y la imperiosa necesidad de desarrollar programas de construcción de viviendas sub-urbanas y rurales, enfrentamos la tarea de la busqueda de un aglomerarte de bajo costo y de facil producción, destinado fundamentalmente a la producción de trabajos de albafiilerfa y otros usos de bajo requerimiento en cuanto a resistencia mecanicas. Como referencia para este trabajo tomamos los cementos naturales producidos en Espafia los cuales con anterioridad se agrupaban en la denominación generica de cemento Zumaya (nombre de la region de Guipuzcua con una tradicional y muy desarrollada industria de los cementos naturales), aglomerantes que han jugado y min juegan importantfsimo papel en la construcción de este país. Baste sefialar que en los afios de crisis energetica durante la II guerra mundial los cementos naturales, llegaron alcanzar el 40% de la producción total de cementos en Espafia.
Todavía a fines de la decada del sesenta la industria cementera Espanola (ya muy desarrollada) con una capacidad instalada para la producción de cementos portland, puzolanicos, de alto homo y siderurgico, asf como aluminosos, de 15, 974 millones de toneladas anuales, producía 646.4 miles de toneladas de cemento natural y 88.2 miles de toneladas de cal hidraulica. Otro tanto ocurre en Francia, en la cual junto a la producción de cementos normalizados, coexiste una vasta industria de otros cementos y aglomerantes.
A modo de ejemplo podemos decir queen 1984 (todavía en proceso de recuperación de la guerra) en Francia se produjeron 5.5 millones de toneladas de cementos, empleandose para ello 1.5 millones de escorias, ademas de 2 millones de toneladas de cales hidraulicas y aglomerantes analogos. Como podemos apreciar la carencia de recursos energeticos ha sido un tremendo estimulante de la producción de estos aglomerantes, que vuelven a ganar la importancia no solo en nuestro país por los mismos motivos: el elevado costo de la energía.
Se parte del criterio de lograr un aglomerante equivalente a los cementos naturales con el menor consumo energetico posible y de acuerdo con la experiencia acumulada a lo largo de los afios en el estudio de las puzolanas y sus reacciones, así como los cementos con adiciones de aquellos, y teniendo en cuenta la experiencia hist6rica de milenios que se hace patente de modo irrefutable en los numerosos panteones, estadios, acueductos, cisternas, puentes y puertos, que han resistido con total exito el intemperismo de mas de 20 siglos, inclusive la agresividad extrema del mar.
A lo anterior se agrega el hecho de que la producción de la cal, inclusive la hidraulica, implica un elevado gasto energetico, pues para la tecnologfa tradicional de producción de cal en homos verticales aun en los disefios y construcciones recientes, el consumo energetico se encuentra en el orden de los 1250 kcal/ kg. de cal producida, magnitud que puede incrementarse en el caso de las cales hidraulicas. Por todo esto se desarrollan los trabajos, inicialmente a nivel de laboratorio a partir de mezclas de puzolana pulverizada hasta finuras del orden de 90% en el tamiz de 0.09 mm. con hidrato de cal (comercial) y posteriormente cal viva en las cuales estas ultimas serfan el componente minoritario.
Caracteristicas
Este aglomerante como su nombre lo indica, esta constituido por una mezcla fntima y homogenea de puzolana mas cal (viva o hidratada) pulverizados hasta finura similar a la del cemento portland y, el mejor modo de lograrlo es la molienda conjunta y adecuadamente dosificada (7080% de puzolana y 30-20% de cal) aunque se puede lograr por molienda separada y ulterior mezclado, pero existen riesgos de no alcanzar una buena homogenización. Las puwlanas no son masque minerales, generalmente silicatos o aluminosilicatos que, careciendo de propiedades cementicias y actividades hidraulicas por si solas, son capaces de reaccionar a temperatura ambiente con la cal o hidróxido de calcio u otras sales calcicas, en presencia de agua, para dar lugar a la formación por via topo qufmica de productos estables y practicamente insolubles con propiedades y características similares a los formados durante el fraguado o hidratación del cemento portland.
En nuestro país existen yacimientos de grandes volumenes de rocas con actividad puzolanica notable: zeolitas y tobas, a la cuales se les agrega otras puzolanas artificiales tales como las arcillas calcinadas (en muchos casos ladrillos, tejas, y otros productos de arcillas cocidas pulverizadas), el "flay ash" o ceniza volante, la ceniza de cascara de arroz (por la sflice amorfa) e incluso las cenizas del bagazo de cafia quemado en los centrales azucareros, aunque con una actividad puzolanica menor que las restantes.
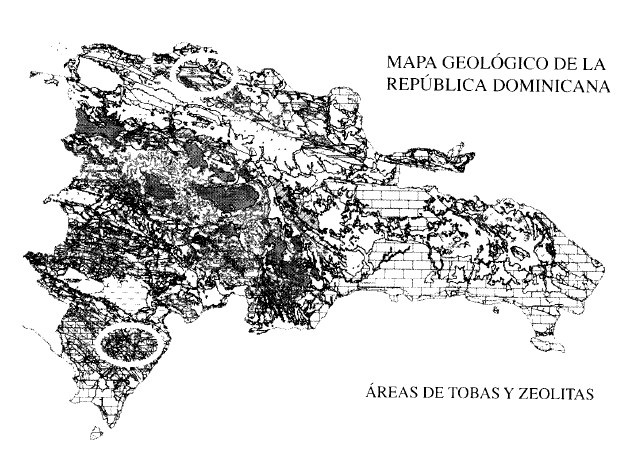
Cabe destacar que tanto la toba de Puerto Plata como la zeolita de Barahona presentan una excelente actividad puzolanica, resultados estos obtenidos siguiendo la norma de muestreo y ensayos descrita en el metodo de Fratini a una población estadfsticamente representativa. Este metodo esta basado en la capacidad de los minerales activos de absorber el hidrato de calcio que se forma como resultado de los procesos de endurecimiento del cemento que se prepara a partir del clinker, las propias puzolanas y el yeso.
La actividad se determina comparando el contenido de hidrato de calcio en la fase lfquida en contacto con el cemento, con el contenido correspondiente al estado de saturación. Mientras menor sea la concentración de hidrato de calcio en la fase liquida en comparación con la concentración del estado saturado, mas activo sera el mineral. Procede aclarar que el efecto puzolanico determinado en este ensayo, no solo es valido para su factibilidad como aglomerante puzolanacal (APC), sino tambien como aditivo en la fabricación de cemento portland puzolanico (ver conclusiones y recomendaciones).
En cuanto a la cal, para la producción del APC, no es requisito obtenerla a nivel industrial con la mas alta pureza, pudiendo emplearse con todo el exito inclusive la obtenida en homos verticales criollos, los cuales si bien no poseen una alta eficiencia termica, en cambio son de muy facil y barata construcción, permitiendo el empleo de residuos y otros combustibles que reducen sensiblemente los costos de producción.
Resulta evidente que las características del aglomerante han de estar en función de la puzolana y la cal disponible, asf como la tecnologfa de producción, razón por la cual, los indicadores generales que a continuación se ofrecen sirven de orientación a quienes se propongan producir sus propios aglomerantes de calpuzolana.
La tarea consiste en determinar las propiedades de uso de cada APC producido a partir de puzolana y cales adecuadamente caracterizadas, fundamentalmente en cuanto a la resistencia mecanica que logren en mortems de APC, empleando para ello la arena disponible en la region, velando que la misma cumpla en la mayor medida con los requerimientos establecidos.
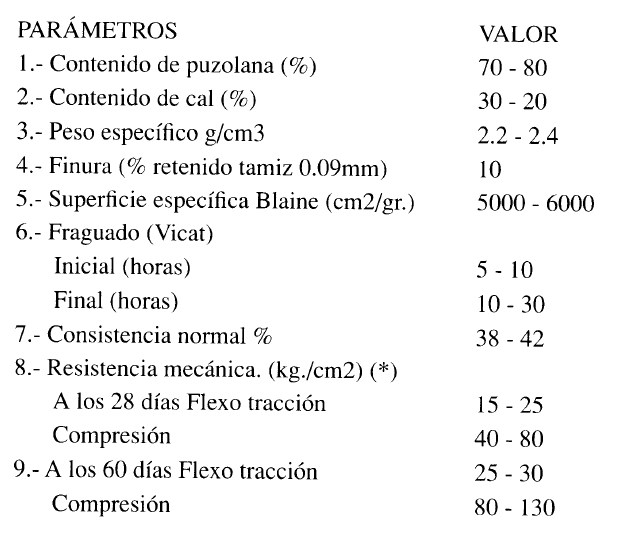
Ensayadas en probetas normadas con proporción aglomerante / arena igual a1/3 y relación agua / aglomerante entre 0.6 y 0.8, curadas bajo agua y ensayadas segun requerimientos establecidos en las normas.
Cuando al APC se le adiciona cemento portland se logran reducir los tiempos de fraguado segun el ensayo Vicat hasta los valores normales para este cemento, a la vez que se incrementan las resistencias a todas las edades y se reduce la necesidad de agua de amasado, ampliandose el campo de aplicación del APC.
Hemos de tener presente en todo momento que el empleo
del APC requiere de maxima atención al curado de los elementos producidos, pues la desecación, tanto del mortero como del hormigón (fundamentalmente en los primeros 7 dfas) provocan la paralización de la reacción de la puzolana con la cal, aunque la adición de cementa portland disminuye este riesgo, pues al ocurrir el fraguado del mismo queda "atrapada" en la estructura formada, cierta cantidad de agua de mas dificil evaporación, aunque siempre se ha de requerir un mayor cuidado en el curado. En el caso del empleo del APC en empafietes para la construcción de muros de blocks o ladrillos ha de tenerse la precaución de que estos se encuentren debidamente humedecidos para evitar que por absorción del agua desequen el mortero.
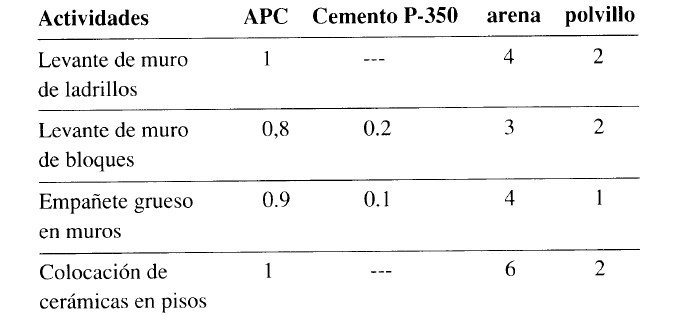
Recomendaciones
1 En las paredes de ladrillos levantados con el mortero de 100% de APC no se podran efectuar trabajos de encofrados hasta despues de 72 horns, o de lo contrario emplear en las ultimas 5 hiladas un mortero con 75% de APC y 15% de cemento portland.
2 Las juntas no deberan exceder de 1.5 cm., preferentemente 1 cm.
3 Las juntas de pisos y enchapes se realizara solo con cemento portland.
4 No se recomienda el APC en empafiete fino en exteriores, pero en interiores podra usarse en base a 60% de APC y 40% de cemento portland.
Evidentemente, podran ser empleadas otras dosificaciones de acuerdo con las necesidades y los materiales disponibles por el constructor (aglomerantes, agregados, elementos a colocar asi como las condiciones ambientales, etc.), sugiriendo la presencia de arena de origen calcareo (polvo de piedra) a los silicios o igneos.
Hormigones
Se trata de hormigones de baja resistencia (del orden de 160kg/cm2 o menor) en los cuales se recomienda el empleo combinado del APC con cementos portland y asf lograr la cohesion necesaria para formar la estructura del hormigón con la resistencia requerida.
Es obvio que la dosificación depende no solamente de la resistencia especifica de aquel y de la marca o resistencia media de este, sino de las caracteristicas de los agregados disponibles, asf como de la laborabilidad requerida, razón por la cual, en el caso de la preparación de hormigones, tanto vaciados "in situ" como de elementos prefabricados sencillos, debe procederse a los ensayos de dosificación previos, recordando que tanto el peso especifico como volumetrico del APC y de sus mezclas con el cementa portland son menores que los de este ultimo y los hormigones resultantes tendran un peso especifico del orden del 5 % menor que los elaborados con el P350.
Experiencias comprobadas en la producción a escala semiindustrial de APC demostraron la posibilidad real de lograr hormigones de hasta f' c = 160 kg./cm2 con mezclas compuestas de 60% de APC y 40% de cementa P350 y una dosificación general de 352 kg./m3, relación agua/cemento = 0.57 y 8 cm. de asentamiento medidos en el cono de Abrams.
Si comparamos los 352 kg. de APC con los 333 kg. de P350 que aproximadamente se utilizan para este tipo de hormigón, vemos que se logra un ahorro energetico importante, pues en este caso se ha empleado solamente 141 kg./m3 de P-350 y los restantes 211 kg./m3 de APC, que tomando en cuenta un consumo energetico 4 veces menor equivalente a 53 kg./m3 de P-350, o sea un total energetico equivalente a 194 kg./m3.
Para mezclas de 50-60% de APC y 50-40% de P-350 y sobre la base de asentamiento de 5-8 cm., las dosificaciones de dichas mezclas de acuerdo con las marcas de hormigones deseadas estarfan en los siguientes órdenes:
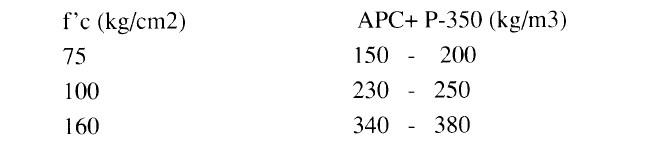
Como aplicación practica de lo anterior tenemos la construcción de aceras y zapatas corridas para paredes de viviendas de blocks y techo aligerado, a partir de 50% de APC y 50% de P-350 obteniendose valores de hasta un f'c = 175 kg./cm2, tambien en elementos de prefabricado de terrazo como son mesetas de cocina, lavaderos y pasos de escalera, logrando su pulido a los dos dfas de producido sin dificultad. En este caso se recomienda el empleo de los elementos (su colocación en obra) despues de los 28 dfas para lograr un alto nivel de reacción entre la puzolana y la cal, garantizando asf su mayor la durabilidad
Blocks de hormigon
El mayor problema que enfrentan la producción de blocks de hormigón huecos esta dado por la fuerte tendencia a la desecación del mismo como consecuencia de la baja relación agua/cemento (es un hormigón de asentamiento cero) y al alto valor de la relación superficie/volumen.
Es por ello que las deficiencias en el curado de los blocks provocan cafdas de resistencia notables, lo cual se agrava por su almacenamiento a pleno sol a las 24 horas de producidos en el mejor de los casos. Como sabemos, existen en nuestro país diversas variedades de bloqueras que van desde totalmente automatizadas con modema tecnologfa de punta, hasta bloqueras criollas o de patio. Aun estas ultimas, cuentan con un area destinada a colocar sobre plantillas o tableros los blocks de la producción del dfa. Cada mafiana antes de reiniciar la producción esta area es despejada y los blocks son trasladados al patio para su almacen definitivo antes de ser despachados no antes de 7 dfas, tiempo en el cual debe lograse la resistencia adecuada para el manejo y el servicio de uso definitivo.
Es recomendable que los blocks se hagan con una mezcla de APC y cemento P-350 al 50% c/u del total del cemento utilizado en condiciones previas normal, aunque en el caso del block de 4" puede aumentarse la proporción de APC. Es importante tener en cuenta que el hormigón preparado debe tener la mayor adición de agua posible que permita la adecuada conformación del bloque por vibración y su ulterior traslado hasta el lugar donde ha de permanecer para su endurecimiento inicial.
El mezclado de la mezcladora debe ser del orden de 2-3 minutos para garantizar la mezcla mas homogenea de los materiales, pues debemos tener presente queen este caso, ademas de cemento portland, grava, arena, agua, tendremos el APC.
La dosificación de la mezcla de APC y cemento P-350 para blocks de 4" es de 1,21,3 kg./block y para los de 6" y 8" de 1.9 2, 1 kg./block, lo cual produce un efecto económico significativo al compararlo con los indicadores de consumo cuando utilizamos como 100% de aglomerante el cemento P-350. Estos blocks hechos con APC y cementa P-350, deben mantenerse durante 24 horns bajo techo con riego de agua despues de esta y con posterioridad durante no menos de otras 72 horns para garantizar el mas eficiente curado de los blocks y con ello lograr las mayores resistencias. El block es un elemento cuyo valor de uso esta definido basicamente por la resistencia a compresión y el tiempo que media entre la producción del elemento y el momento en que alcanza su valor de uso puede incrementarse a mas de 7 dias, lo cual obligaria a pensar en incrementar las areas de almacen para de esta forma no limitar la capacidad de producción.
Ladrillos prensados
Estos elementos de pared son dimensionalmente similares a los producidos en las alfarerias por medio de la tecnica de cocción en homos. En este caso son prensados solamente mediante la utilización de energia hidraulica o electrica utilizando para ello las mismas maquinas usadas en la elaboración del mosaico tradicional, prensando verticalmente el material utilizado a traves de un pisón que se desliza dentro del molde hasta lograr su medida definitiva.
Los ladrillos prensados de acuerdo a su composición se producen con la combinación dosificada de materiales inherentes y adherentes entre los que se pueden encontrar:
Inertes: Polvo de piedra (arena triturada no lavada), residuo de cantera o suelo estabilizado.
Adherente: Cemento portland o cemento portland + aglomerante puzolana cal.
Para cualquier dosificación dada, tanto de aglomerante como de agregados, el factor mas importante lo constituye la presión aplicada, pues la resistencia alcanzada en el elemento depende en gran medida de esta, sin descuidar el curado y la adecuada manipulación del producto. Para ladrillos prensados, aplicando presión de 150 kg./cm2 durante la conformación, se puede emplear una dosificación de 10% de APC con 90% de polvo de piedra y lograr resistencias del orden de los 100 a 120 kg./cm2 requiriendose el curado durante una semana en ambientes humedos bajo techo y posteriormente a las areas de almacenamiento hasta los 14 dfas para su transportación y empleo. Cuando utilizamos cementa portland, estos tiempos son disminuidos.
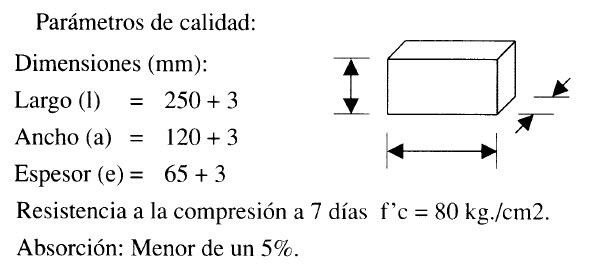
Los atributos de calidad que se deben de controlar y restringir son:
Alabeo o torcedura: Desviaciones en el centro de la cara con respecto al piano divisorio.
Desconchado: Perdida de una porción de la superficie. Despuntado: Rotura de una de las esquinas del ladrillo.
Otros empleos
Actualmente, se han realizados trabajos de investigación sabre el empleo del APC en la estabilización de suelos con resultados positivos; siendo importante sefialar el empleo de hormigones de cenizas volantes cal de consistencia de tierra humeda compactados, como base de pavimentos semiflexibles de carreteras, autopistas, pistas de aterrizajes, parqueos, etc., con dosificaciones de 15-20 % de APC, recordando que en este caso las cenizas volantes no son mas que puzolanas artificiales. En Europa (Espafia y Alemania), muchas carreteras estan hechas con hormigones a base de puwlanas naturales y cal compactada.
Tecnologia de produccion
La producción del APC en plantas pequefias y con rendimientos de 1-3 t/h no es solo posible sino totalmente justificado y recomendado a partir de la concepción de un empleo de dicho aglomerante, que evite las implicaciones de la transportación.
El proceso productivo del APC consta de las siguientes etapas:
1Explotación del yacimiento de puzolana, el cual puede realizarse en muchos casos con un limitado empleo de explosivo o prescindiendo completamente de ello.
2Trituración de la puzolana, la cual puede incluir la necesidad de remolida para lograr una granulometrfa inferior a 10-6 mm. Puede ser realizada en cualquier instalación de trituración de agregados existente, pues cualquiera de ellas dispone de capacidades 20-30 veces superiores a los niveles de producción de estas pequefias plantas. Esto puede implicar la decision de montar la planta próxima a una instalación de trituración ya existente.
3Secado: en ocasiones, la puzolana proveniente del yacimiento posee una humedad tal, que una vez triturada no es posible proceder de modo inmediato a su molienda fina, razón por la cual ha de requerir un secado previo, que es factible mediante la energía solar, tanto por secado directo, por exposición al sol como mediante secadores especiales disefiados para ello.
4Molienda: es recomendable en un molino de bolas debido a los requerimientos de finura del APC y preferentemente de modo conjunto la puzolana y la cal. Dadas las capacidades fijadas, la construcción de un molino de bolas de 1 6 2 camaras de flujo continua no ofrece grandes dificultades. Esta etapa de molienda es decisiva en el proceso, debiendo prestarse la maxima atención a la dosificación de la puzolana y la cal, requiriendo en el caso de molienda continua de un sistema de control de alimentación adecuado.
5Producción de cal, en homos verticales tradicionales alimentados con roca caliza triturada de dimensiones del orden de 50-80 mm. utilizando algun combustible alternativo como es tradicional en esta producción. Preferentemente debe usarse la cal viva en molienda conjunta con la puzolana, teniendo cuidado que no se vea expuesta a la lluvia, resultando mas ventajoso y menos molesto que la manipulación del hidrato de cal. En todo caso sera necesario separar las partfculas de calizas mayores de 10mm no calcinadas (huesos), lo cual puede hacerse por tamizado manual o mecanico o en su lugar someter la cal a trituración previa a la molienda.
6 Almacenamiento y entrega. Aunque pueden emplearse diversas variantes, la mas 1ógica es el almacenamiento en un silo o tolva cubierta que proteja al APC de la meteorización. Esto implica la solución de llevar el APC desde la descarga del molino de silo; lo cual puede ser afectado mediante un elevador de cangilones, una banda transportadora o un sistema neumatico, todos de pequefias dimensiones. Los silos o tolvas han de tener capacidad para un mfnimo de 3 dfas de producción y preferentemente dos, para que mientras uno recibe el APC que se este produciendo, la entrega la realice el otro, cuya producción ya ha sido evaluada a lo largo del proceso, lo cual ha de garantizar la calidad del producto. La entrega podra hacerse a granel, de modo similar al cemento, o en sacos, empleandose para esto ultimo las ensacadoras de sinfin usadas en el hidrato de cal o en el yeso. Dadas las características de los sólidos pulverizados, los cuales tienden a sufrir apelmazamiento, se recomienda, disponer de un pequefio compresor y una red de aire comprimido.
Esquema del proceso de producción del aglomerante de calpuzolana.
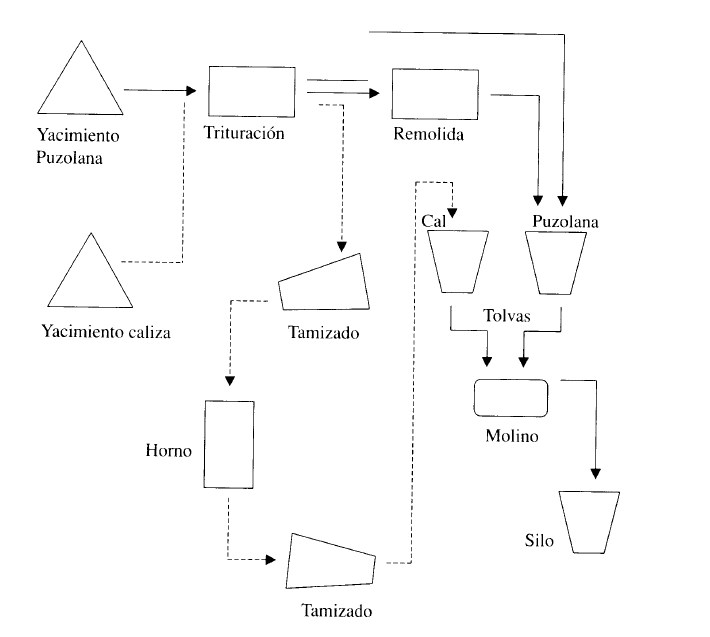
PINTURA CEMENTOSA
Definicion
Esta pintura producida en forma de polvo seco, esta constituido por una base cementosa, que al ser mezclada con agua, permite obtener un revestimiento con propiedades impermeabilizantes que decora todo tipo de superficie de hormigón, mortero, piedra, ladrillo y block, pudiendo usarse tanto en interiores como en exteriores.
Indicaciones de uso
Preparación de la superficie:
Debe estar libre de polvo, grasa, sales y esflorecencias. Para aplicarla en una superficie ya cubierta con otros tipos de pintura, debe ser rapillada para eliminar todo el material suelto. Por ultimo, debe humedecerse la superficie hasta su saturación para evitar la absorción del agua contenida en la pintura.
Preparación de la pintura:
Se mezcla un volumen de polvo con igual volumen de agua, por ejemplo, para un galón de polvo, un galón de agua. Es apta para su uso hasta dos horas despues de mezclada, pasado este tiempo, comienza a endurecerse. El mezclado debe hacerse echandole el polvo al agua poco a poco e ir batiendo constantemente hasta obtener la homogeneidad requerida. Despues del mezclado, la pintura se deja reposar durante 15 minutos al cabo de los cuales se bate nuevamente, se pasa por una malla para mosquito y ya esta apta para su aplicación.
Aplicación:
Al aplicarse en exteriores, es recomendable pintar los frentes que no reciban el solo en los momentos de menor intensidad del mismo, evitando en lo posible las horas del medio dfa. Puede ser aplicada con brocha, con pistola de aire comprimido o con rodillo de espuma.
Antes de iniciar la aplicación, debe verificarse que la superficie se mantiene humeda. Para aplicar la segunda mano, se debe esperar 24 horas, humedeciendo de nuevo la superficie.
advertencias:
No se aplica sobre madera, metal ni paredes estucadas.
No debe agregarsele agua a la pintura una vez preparada.
El empleo de esta pintura, no debe exceder de los seis meses posteriores a su fabricación.
Para el almacenamiento de este producto, deben cumplirse las mismas reglamentaciones y precauciones que se siguen con el cementa.
Preparacion y aplicacion de la pintura cementosa
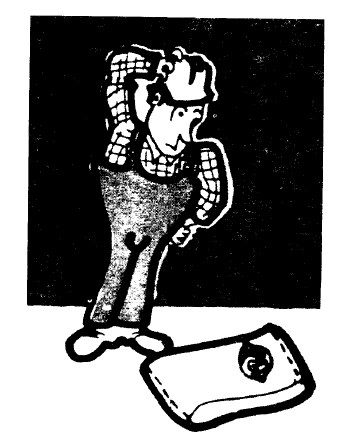
La pintura cementosa es un acabado superficial, compuesto por polvo seco de cementa portland blanco, pigmentos y otros materiales organicos e inorganicos, los que mezclados con agua, en el momenta de su aplicación, producen una capa milimetrica de protección en hormigones, mortems y otros materiales similares.
La durabilidad, en exteriores, es de diez afios y para lograrlo es necesario un estricto control de calidad de las materias primas del producto terminado y de la aplicación en obra.
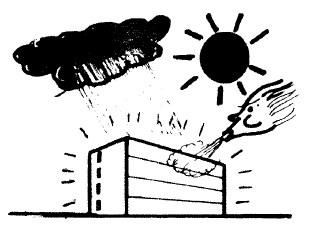
El material es envasado en forma de polvo en fundas multicapas valvulados de papel kratf hasta un peso de 32 kg. lo que equivale, despues de la adición del agua en obra a 48 litros de pintura liquida.
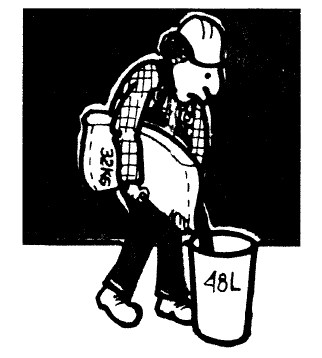
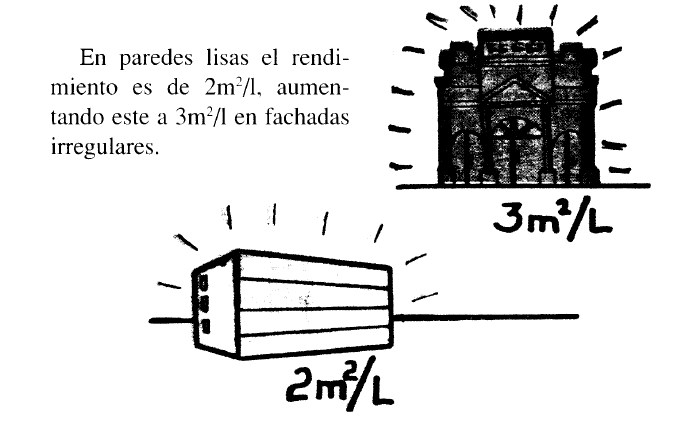
Estas deben limpiarse de polvo, grasas y de cualquier tipo de eflorescencia o de partfculas sueltas, y si anteriormente estaban cubiertas con otros tipos de pinturas se elimina, mediante el rapillado, de todo lo que este suelto o removible, hay que humedecerlas intensamente con abundante agua 15 minutos antes de comenzar a aplicar la pintura.
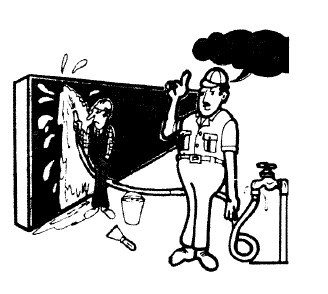
Se mezcla un volumen de polvo seco con un volumen de agua. Este mezclado debe hacerse echandole el polvo al agua lentamente y agitando de forma continua hasta obtener una pasta homogenea. Despues, esta mezcla se deja reposar durante 15 minutos al cabo de los cuales se agita nuevamente y se pasa por una malla fina quedando lista para su aplicación.
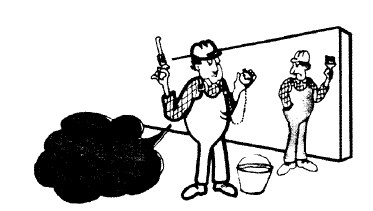
Antes de iniciarse la aplicación, siempre debe verificarse que la superficie se mantenga humeda; se puede pintar con brocha, pistola de aire comprimido o con rodillo de espuma. Al trabajarse los exteriores, es recomendable pintar las fachadas cuando no reciban el sol o en los momentos de menor intensidad, evitando las horns del medio dfa. Con altas temperaturas hay que evitar la rapida evaporación del agua.
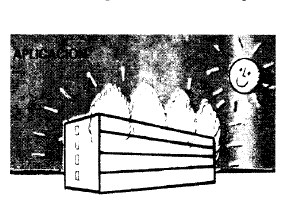
Con la cantidad preparada se puede pintar hasta 3 horns ya que pasado este tiernpo cornienza a endurecerse y no puede agregarsele agua.
Es aplicable tanto en exteriores corno en interiores y posee una serie de ventajas.
Garantiza la protección hidrófuga de la superficie.
Puede ernplearse para cualquier tipo de superficie exceptuando las de rnaderas, las rnetalicas y los estucos.
Con solo aplicar dos rnanos de esta pintura se logra una terminación adecuada.
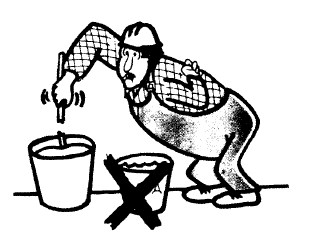
La posibilidad de incorporarle pigrnentos inorganicos perrnite que esta se pueda ofrecer en la garna de colores siguientes: blanco, crerna, arnarillo, rosa, azul claro, verde claro y azul colonial.
La mezcla de pintura pigrnentada requiere 1/3 mas de agua en su preparación que la de color blanco.
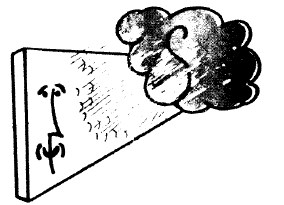
Este acabado requiere de una gran destreza y curiosidad del operario para que la superficie no quede rallada por el paso desordenado de la brocha.
Siernpre deba aplicarse de arriba hacia abajo.
Para aplicar la segunda Q rnano debe esperarse 24 horas y hurnedecer la superficie igual que la prirnera.
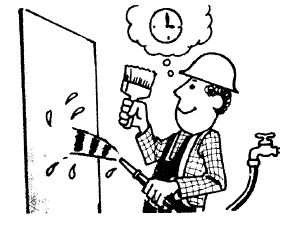
Proceso productivo
Descripción de! proceso tecnológico:
Características generales:
La producción de pintura cementosa, es un proceso fisico químico, que se obtiene a partir del mezclado en forma dosificada en seco, de las diferentes materias primas que la componen, hasta lograr una correcta homogenización de todos sus componentes, que le confieren cualidades como pintura.
Etapas en que se divide el proceso:
Ira Etapa: Tamizado y dosificación de las materias primas. 2da Etapa: Mezclado de las materias primas.
3ra Etapa: Envase y almacenamiento del producto terminado.
Descripción de las etapas:
Ira Etapa: Tamizado y dosificación de las materias primas.
Objetivos: Establecer el control de las especificaciones de calidad de las materias primas, su almacenaje, tamizado y dosificación de los diferentes componentes.
Operaciones tecnológicas de la etapa.
a) Limpieza de los equipos tecnológicos.
b) Pesada de las materias primas.
c) Tamizado de las materias primas.
Descripción de las operaciones tecnológicas.
A) Limpieza de los equipos tecnológicos.
Consiste en eliminar los residuos de la mezcla que permanezcan en el mezclador y tolva una vez descargada esta. La frecuencia de esta operación es cuando se produzcan cambios de colores.
B) Pesada de las materias primas.
Esta operación, se realiza para medir con exactitud las cantidades de materias primas para posterior elaboración de la mezcla, con lo que se obtiene la pintura.
Las materias primas utilizadas son todas de producción nacional o adquirida en el mercado local, cumpliendo por igual las especificaciones de calidad relacionadas a continuación y exigidas para la elaboración del producto.
Dosificaciones utilizadas: las formulas en %, asf como las cantidades para una bachada de 1000 kg. y de 1200 kg, aparecen en el siguiente cuadro:
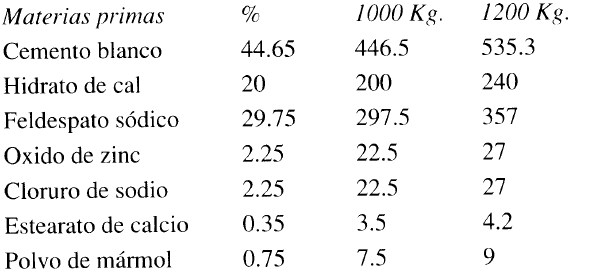
Especificaciones de calidad de las materias primas:
Cemento: Se tamizara una zaranda con una malla de 0.5 mm. Sera blanco con una resistencia de 400 kg. /cm2 a 28 dias.
Hidrato de cal: Ca (OH)2 cal apagada o hidróxido de calcio. La calidad tecnica con que viene embasada es correcta yen muy raras ocasiones habra que tamizarla. El contenido de pureza mfnimo sera de 90 % y con un contenido de 6xido de calcio y 6xido de magnesia total libre no mayor que el 8 %.
Feldespato de sodio, no presentara impurezas, estara libre de humedad y pasara por el tamiz de 1,19 mm. y retendra como minimo un 95% en el tamiz de 0,149 mm. y un contenido maximo de óxido de hierro de I%.
Cloruro de sodio: utilizar solamente sal fina comun, no se puede utilizar ningun tipo de sal de grano grueso, pues esta contiene un porcentaje de humedad no aceptado en la producción de pinturas a base de cemento.
Polvo de marmol: tiene que estar totalmente seco, lo cual puede lograrse por secado en homo o secado natural. Al igual que las materias primas anteriores, se tamizara por una malla de 0.5 mm.
Estearato: Este producto no necesita ninguna preparación previa antes de su uso. Existen tres tipos que pueden utilizarse: estearato de calcio, de aluminio o de zinc, cuyas propiedades hidrófugas (repelencia al agua) disminuyen en ese mismo orden. Se recomienda usar el primero para alcanzar una mayor impermeabilidad de la pintura cementosa. Por sus caracteristicas, un dosificado en exceso, anula totalmente la pintura al no poder ser mezclada con agua.
6xido de zinc: puede utilizarse tal y como viene envasado. Debe ser pasante por el tamiz 1.19 mm.
Pigmentos: solo pueden utilizarse 6xidos metalicos pues los pigmentos organicos no son compatibles con los otros productos de la pintura. Se utilizara la cantidad establecida para la gama de colores que se desee obtener expresados en% con relación al peso del cemento.
c) Tamizado de las materias primas.
Es el proceso mediante el cual se garantiza la granulometrfa de los diferentes productos, en relación al tamafio maximo.
2da Etapa: Mezclado de las materias primas:
Objetivo: El objetivo de esta etapa es mezclar los diferentes componentes de la pintura en un mezclador de doble batida, hasta obtener el grado de homogenización requerido.
Operaciones tecnológicas de la etapa:
a) Vertido de los diferentes materiales segun su orden.
Mezclado de los materiales.
Descarga de la mezcla hacia la tolva receptora. Descripción de las operaciones tecnológicas:
a) Vertido de los diferentes materiales segun su orden.
Despues de pesadas las materias primas, segun el cuadro de dosificaciones y tamizadas, se procede a verter el producto en el siguiente orden:
En la tolva de llenado:
Hidrato de cal.
Cementa blanco.
Feldespato sódico.
Se transporta el 50% de estos componentes, mediante un elevador de canjilones hasta el mezclador de doble batida, mezclandolo durante 3 minutos. Seguidamente se afiade el resto de los productos (aditivos y pigmentos), directamente a traves de la compuerta o tapa del mezclador. Estos son:
óxido de zinc.
Estearato de calcio.
Cloruro de sodio.
Polvo de marmol.
Pigmentos.
Posteriormente se completa con el 50% restante del cementa, feldespato e hidrato de cal.
a) Mezclado de los materiales.
Una vez unidos todos los componentes de la pintura en el mezclador de doble batida, se comienza la operación de mezclado de estos productos durante 1 hora, tiempo en que se debe alcanzar el grado de homogenización requerido, tanto en pintura blanca o de color.
c) Descarga de la mezcla hacia la tolva receptora. Concluido el tiempo de mezclado en el molino de doble batida, se comienza la descarga del producto hacia la tolva receptora, pasando el mismo por el molino de disco a fin de lograr que se mantenga el grado de finura establecido para la pintura.
3ra Etapa: Envase y almacenamiento def producto terminado.
Objetivo: El objetivo de esta etapa es: Envasar la pintura en fundas de papel multicapas valvulares. Almacenar el producto terminado envasado. Realizar el control de calidad del producto terminado de acuerdo a las Especificaciones de Calidad y Metodo de Ensayos, relacionados en este trabajo.
Operaciones tecnológicas de la etapa.
a) Envase del producto terminado.
b) Almacenamiento del producto terminado Descripción de las operaciones tecnológicas.
a) Envasado del producto terminado:
Al concluirse el tiempo indicado para el batido y descargado en la tolva receptora, se comienza el llenado de las fundas.
Las fundas seran de papel multicapas valvulados los que seran llenados hasta alcanzar un peso de (32 + 0.5) kg, lograndose a traves de la colocacion de la funda en el extremo de sinffn o gusano llenador.
Cada funda llevara una etiqueta con los siguientes datos: Marca comercial. Nombre generico del producto. Color. Pecha de fabricacion. lndicaciones de uso.
b) Almacenamiento del producto terminado. Se almacenaran las fundas en locales cerrados secos, situandolos sobre paletas de madera con una separacion minima de 10 cm. de la pared. La altura no sera mayor de 3 paletas de 25 fundas cada una.
Control del proceso tecnologico
Puntos de inspeccion:
Inspeccion 1: Control de calidad de las materias primas.
Inspeccion 2: Supervision de la limpieza de equipos tecnologicos.
Inspeccion 3: Supervision de las pesadas.
Inspeccion 4: Supervision del tamizado de las materias pnmas.
Inspeccion 5: Orden del vertido de los materiales.
Inspeccion 6: Supervision del tiempo de mezclado.
Inspeccion 7: Control de calidad del producto terminado por el laboratorio.
Inspeccion 8: Control de las pesadas del producto terminado en fundas.
Inspeccion 9: Supervision al almacenamiento del producto terminado.
Diagrama General de rota
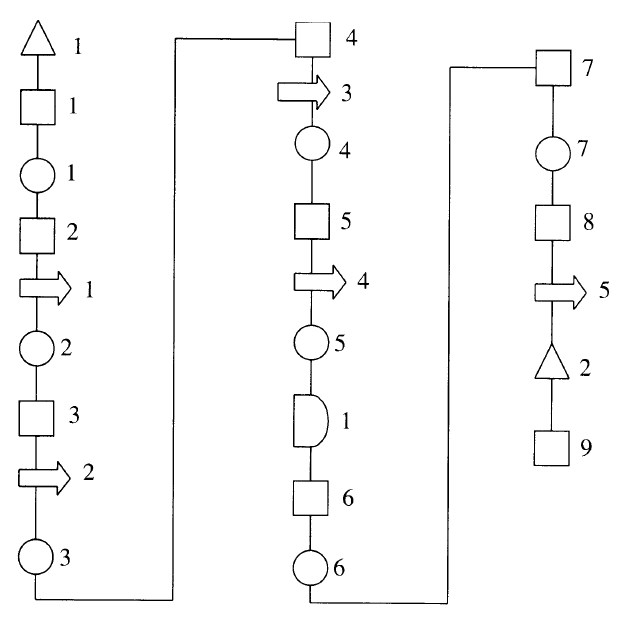
Leyenda. Diagrama General de Ruta
Almacenamiento 1: Almacenamiento de las materias primas. Inspección 1: Control de calidad de las materias primas.
Operación 1: Limpieza de los equipos tecnológicos.
Inspección 2: Control de la limpieza de los equipos tecnológicos.
Transporte 1: Transporte de la materia prima del almacenamiento a la pesa.
Operación 2: Pesada y dosificada. Inspección 3: Control de la pesada.
Trasporte 2: Traslado del producto pesado al tamizado. Operación 3: Tamizado.
Inspección 4: Control del tamizado.
Transporte 3: Traslado de la materia prima a la tolva.
Operación 4: Vertido de las materias primas en la segun su orden.
Inspección 5: Orden de vertido de las materias primas para ser mezcladas.
Transporte 4: Transportación de los materiales de la tolva hacia la mezcladora.
Operación 5: Mezclado de los materiales. Tiempo 1: Tiempo de mezclado.
Inspección 6: Control del tiempo de mezclado.
Operación 6: Descarga de la mezcla hacia la tolva receptora.
Inspección 7: Control de la calidad al producto terminado por media de ensayos.
Operación 8: Envasar la pintura en fundas de papel.
Inspección 8: Control de las pesadas de las fundas (cada 10 fundas).
Transporte 5: Traslado de las fundas en paletas hacia el area de almacenamiento.
Almacenamiento 2: Almacenamiento de las fundas en paletas.
Inspección 9: Control al almacenamiento del producto terminado en fundas y evaluación general de la calidad.
ESPECIFICACIONES DE CALIDAD DE LA PINTURA CEMENTOSA
Los indices de calidad expresados en el siguiente cuadro, representan las variables a ser ensayadas a nivel de laboratorio, las mismas se realizaran segun la norma de muestreo y ensayos existentes para cada fndice, que incluye ademas la normativa para la preparación del mortero base, el vertido y terminación de este en un molde de (20 x 30 x 3) cm. y la preparación y aplicación de la pintura.
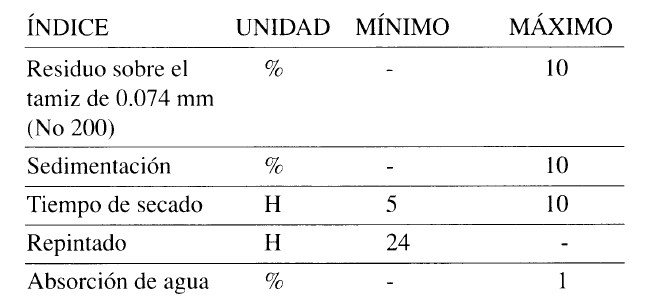
El caleo es un atributo de calidad que consiste en la afectación producida en la superficie pintada caracterizada por el desprendimiento de la pintura en forma de polvo. Esta prueba se realiza de manera practica deslizando el dedo fndice sobre la superficie despues de las 72 horas de aplicada, no debiendo presentar ningun tipo de desprendimiento.
CONCLUSIONES Y RECOMENDACIONES
La factibilidad tanto tecnica como económica de utilizar materias primas nacionales para la producción y uso de estos dos nuevos materiales de construcción presentados (el aglomerantepuzolana cal y la pintura cementosa) abre sin dudas la posibilidad de usar estos ultimos como verdaderos materiales de bajo costo para la construcción de viviendas económicas en nuestro país.
En el caso del aglomerante, el efecto económico se obtiene al poder contar con un material cementante de un costo energetico sumamente bajo, que si bien es cierto posee limitaciones, las bondades del mismo, permiten, como vimos en el desarrollo del trabajo, utilizarlo en numerosos renglones que componen la construcción de una vivienda. Como valor agregado, el contar con grandes yacimientos de minerales de alta actividad puzolanica, (la toba de Puerto Plata y la Zeolita de Barahona) nos permite recomendar, al margen de este trabajo, evaluar la producción industrial paralela de cemento portland-puzolanico a las dos fabricas de ciclo completo (obtención de clinker) existente en el país. Cabe destacar que este cemento es producido por varios paf ses del Caribe, su unica limitante son las resistencias altas a edades tempranas, no existiendo ninguna diferencia de calidad con el portland normal, en de albafiilerfa, etc., lo cual representa mas del 80 % del uso del cemento. Esto permitirfa sin dudas producir un cemento industrial mas económico por concepto de consumo energetico (al usar materias primas mas fundentes) favoreciendo de esta forma a todo el sector de la construcción.
En el caso de la pintura cementosa, el uso sostenido en países como Espafia y Cuba desde la decada de los 80 en proyectos habitacionales rurales o de la periferia urbana, hablan por si solo de su conveniencia, pues salvando los inconvenientes de su preparación y aplicación antes descritos, esta pintura, sin menoscabo de la calidad o durabilidad, tiene un excelente indicador costo rendimiento, constituyendola en una opción verdaderamente competitiva al ser comparada con las pinturas tradicionales.
El objetivo trazado, cumplido con el desarrollo de este trabajo, se coronarfa con el exito si las instituciones y empresas en coordinación con las autoridades competentes del sector, llevaran a vías de hecho este proyecto, es decir, la producción industrial y el uso masivo de estos materiales en la construcción de viviendas económicas. De ser asf estarfamos aportando una pequefia, pero importante cuota en la solución habitacional destinada a la población de menos recursos de nuestro país.
BIBLIOGRAFIA
Calleja. J.: "Código de una buena practica para la utilización de los cementos del Pliego RC-75". Instituto Eduardo Torroja, Madrid. 1997.
Rabilero y J. Muñoz.: "Los aglomerantes en la construcción y sus implicaciones energeticas" IV Congreso Panamericano de Energia xx Convención UPADI 88. La Habana.
Lafuma, H.: "Problemas teóricos de la doctrina de los cementos". Instituto Tecnológico de la Construcción y Cemento. No. 98. Madrid.
Compafifa Espanola de Puzolanas, S.A.: "Conglomerantes puzolanicos: Propiedades y Aplicaciones". Madrid. 1987. NC 54-358: 1986 Norma Cubana. Materiales y Productos de la Construcción. Evaluación de las Puzolanas para la Producción de Aglomerantes. Metodo de Frantini.
NC 54-349: 1986 Norma Cubana. Materiales y Productos de la Construcción. Pintura Cementosa. Especificaciones de Calidad.
Rodríguez M. y Toirac J.: Introducción de la Pintura Cementosa en la Empresa de Materiales de Construcción No 12. Holguin. Cuba. Producción y Uso. Simposio UNAICC. Habana 1987.